My third guitar is a 660mm scale flamenco blanca and like the last one, it’s based on Courtnall’s Barbero flamenco plan, with an eye on Courtnall’s 1933 Santos Hernandez plan and Brune’s 1951 Barbero plan, too. Like the previous two, it took me about six months to complete during evenings, weekends and holidays. I was asked to make it for Rob Johns, my guitar teacher, who liked the previous instrument that I had made for myself. As it happened, I loaned him #2 for much of the time I was working on #3, so it was nice to deliver his guitar and have my own back.
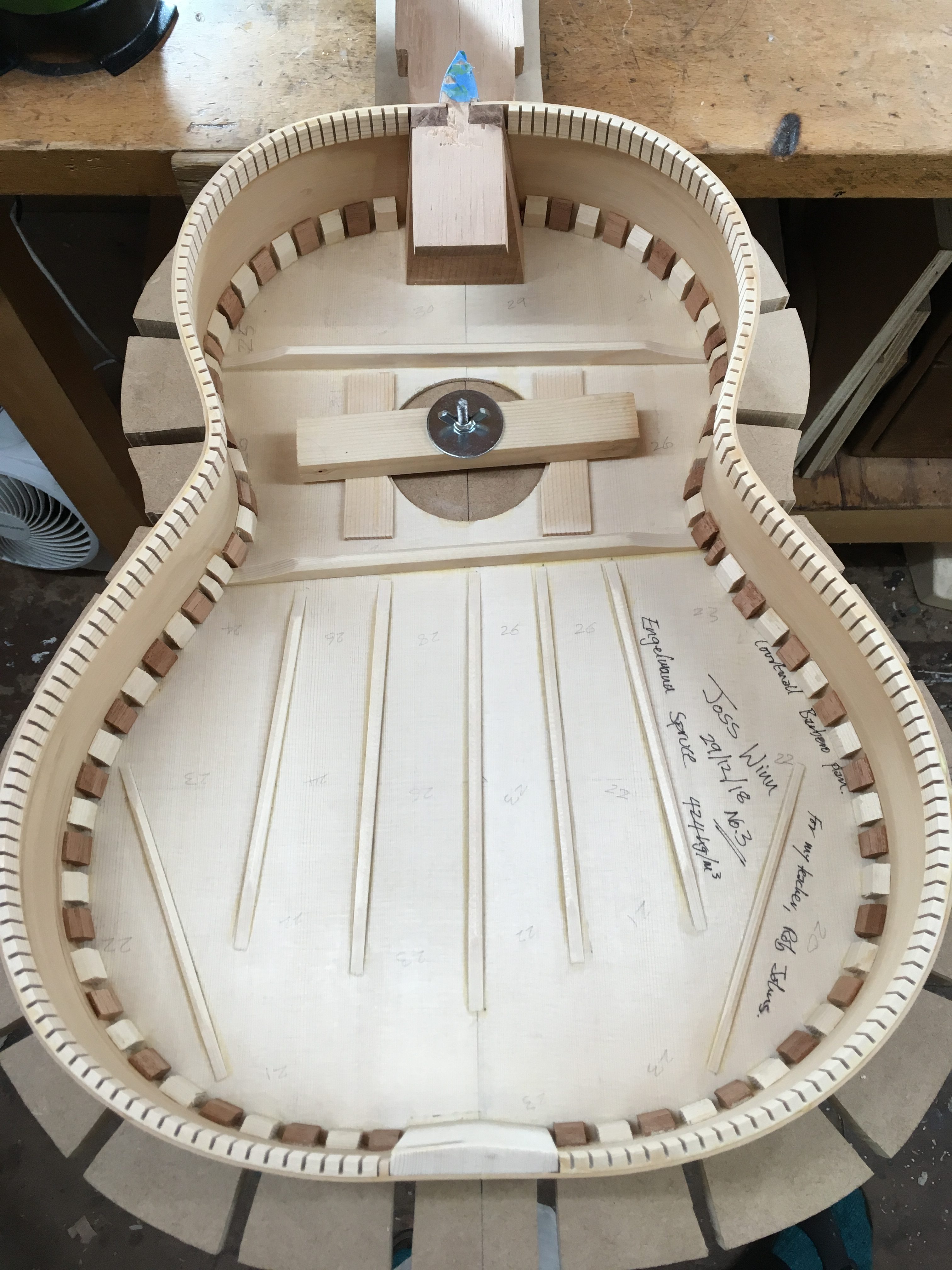
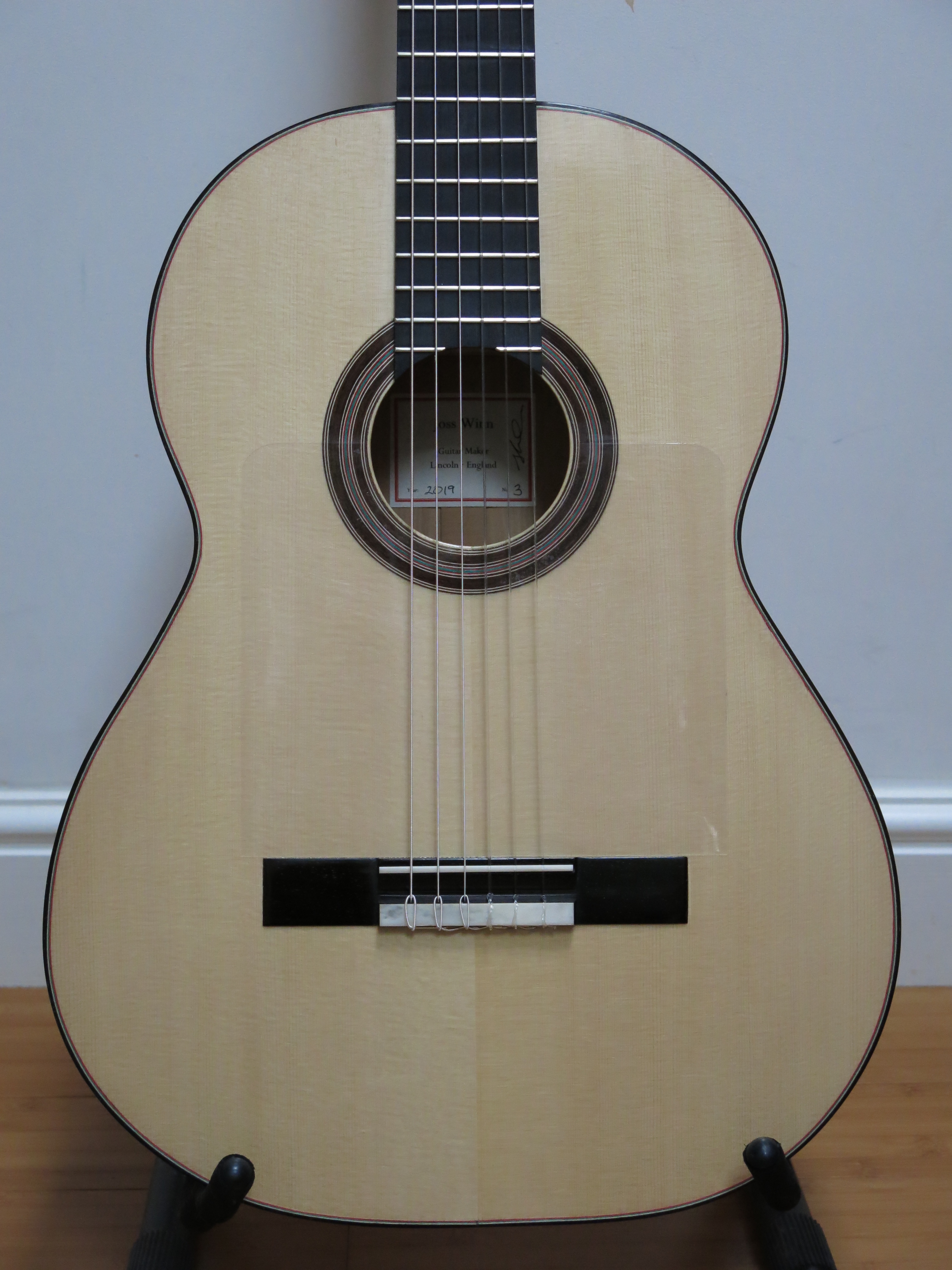
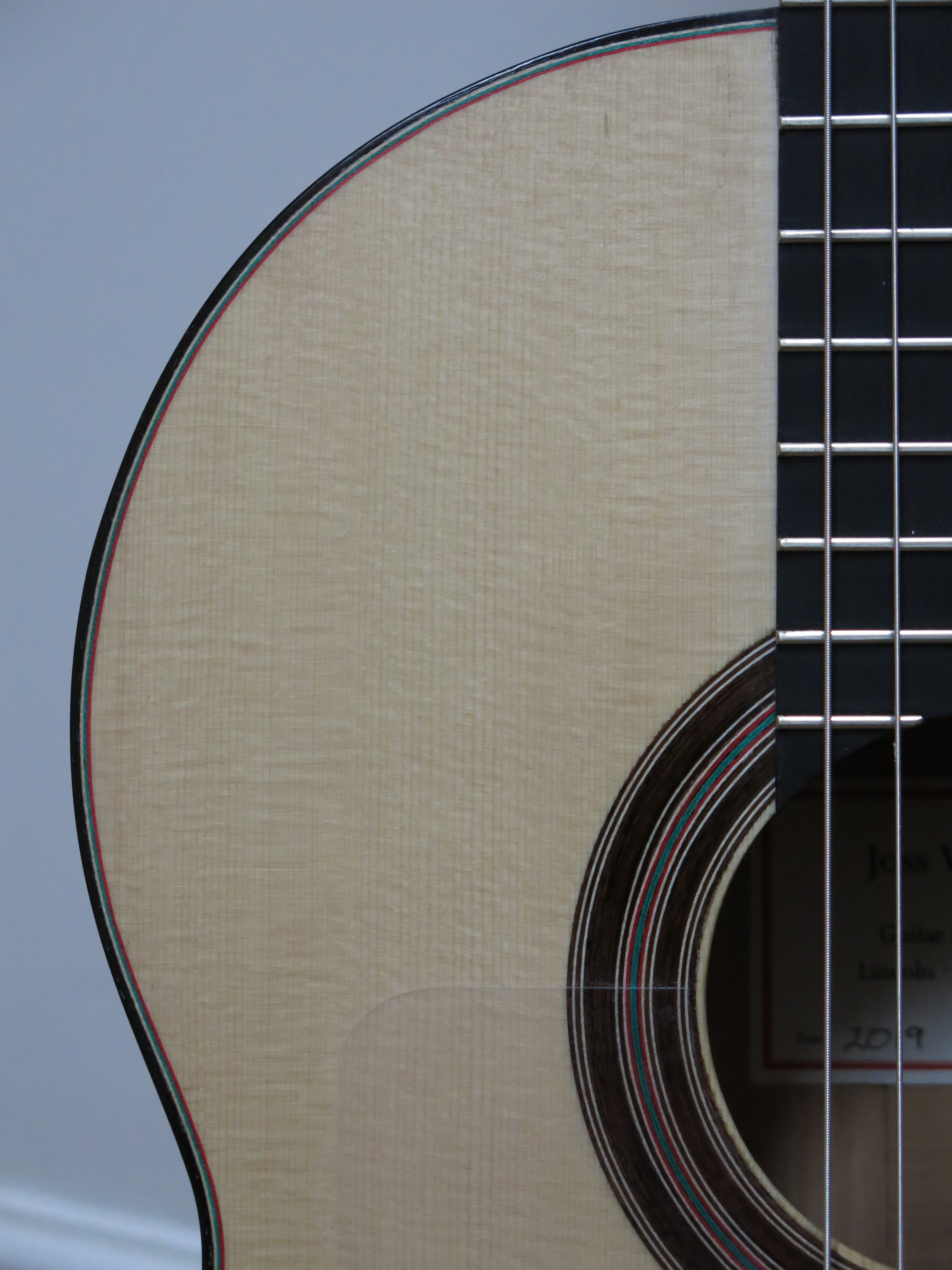
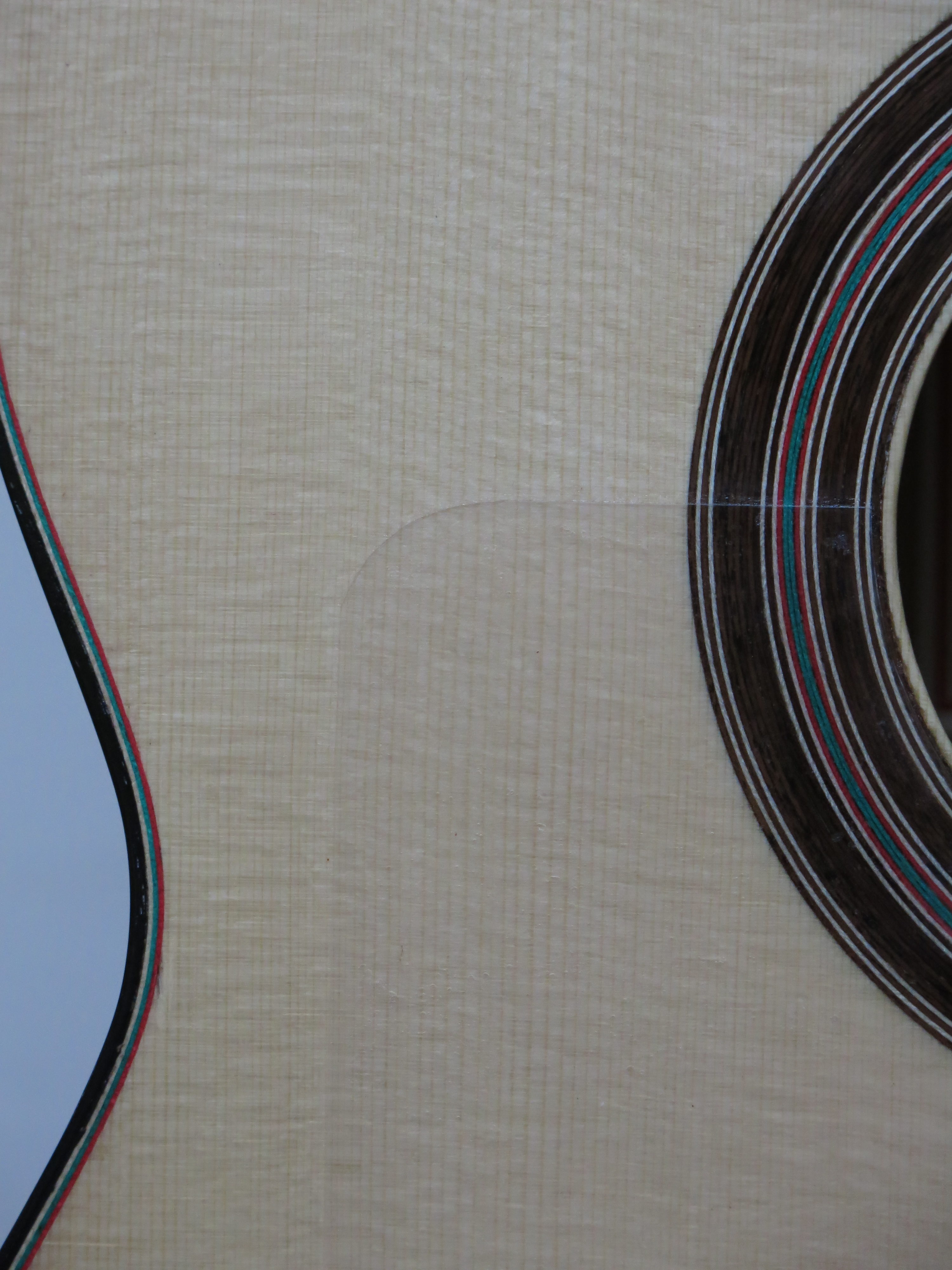
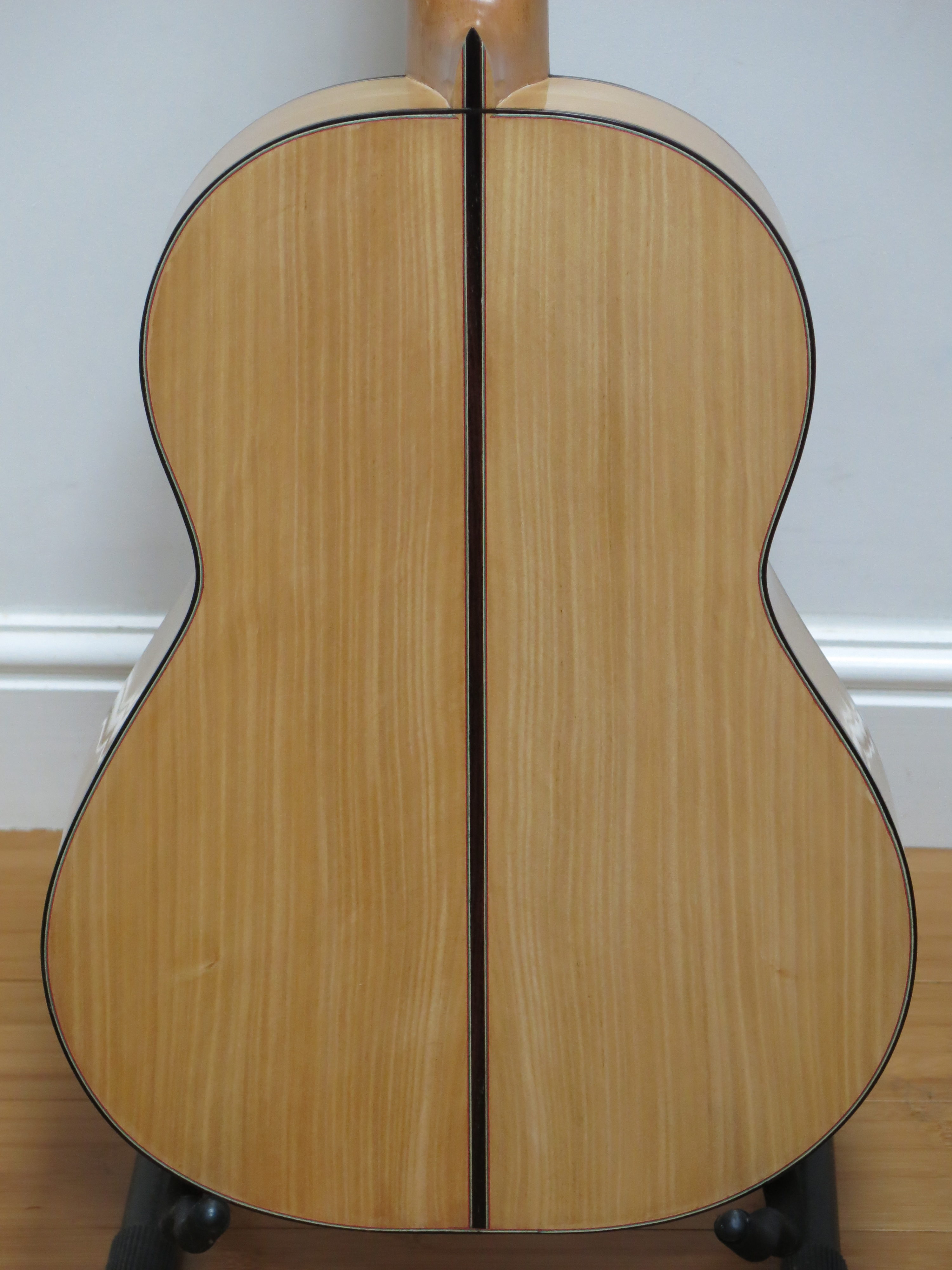
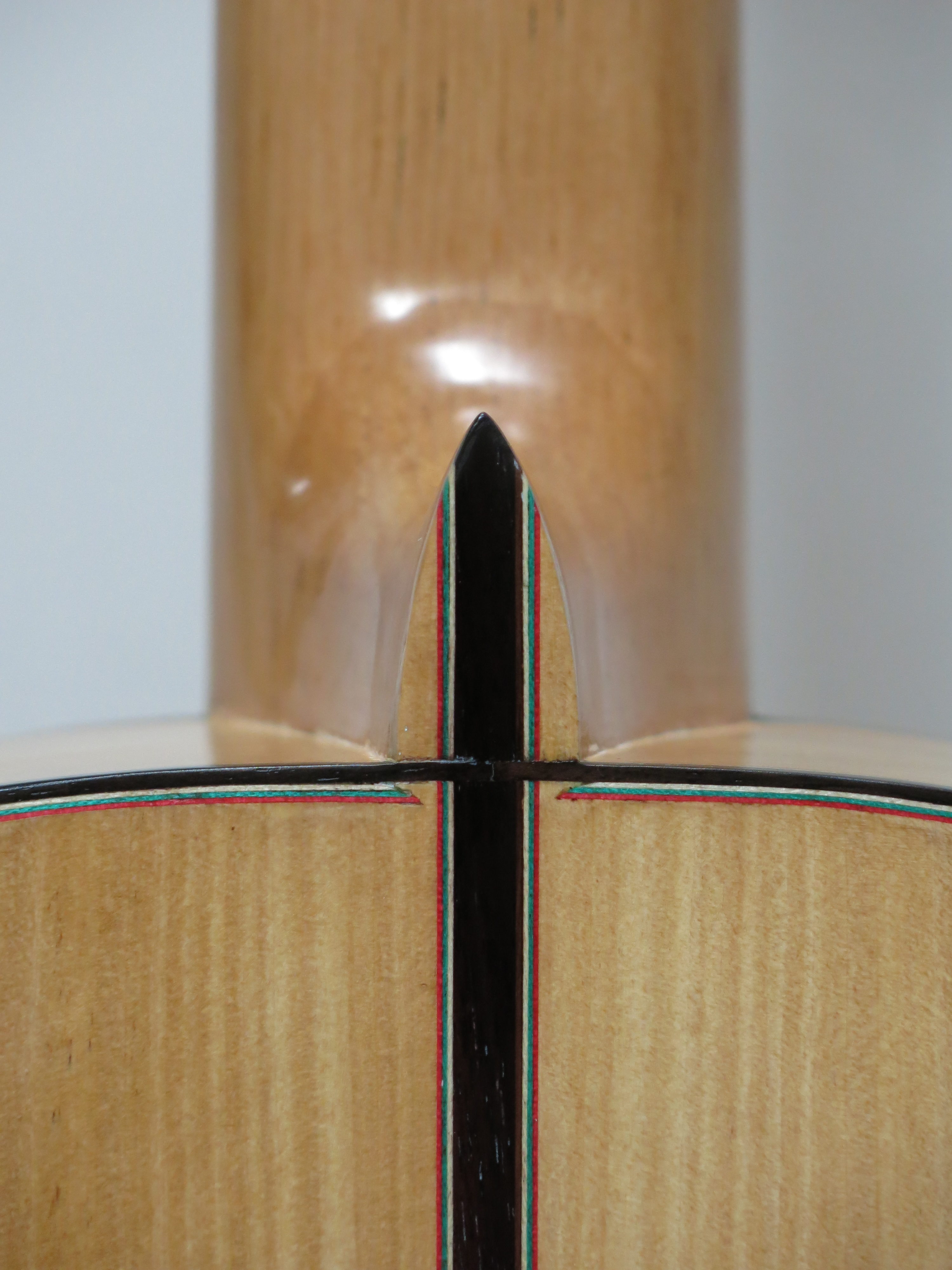
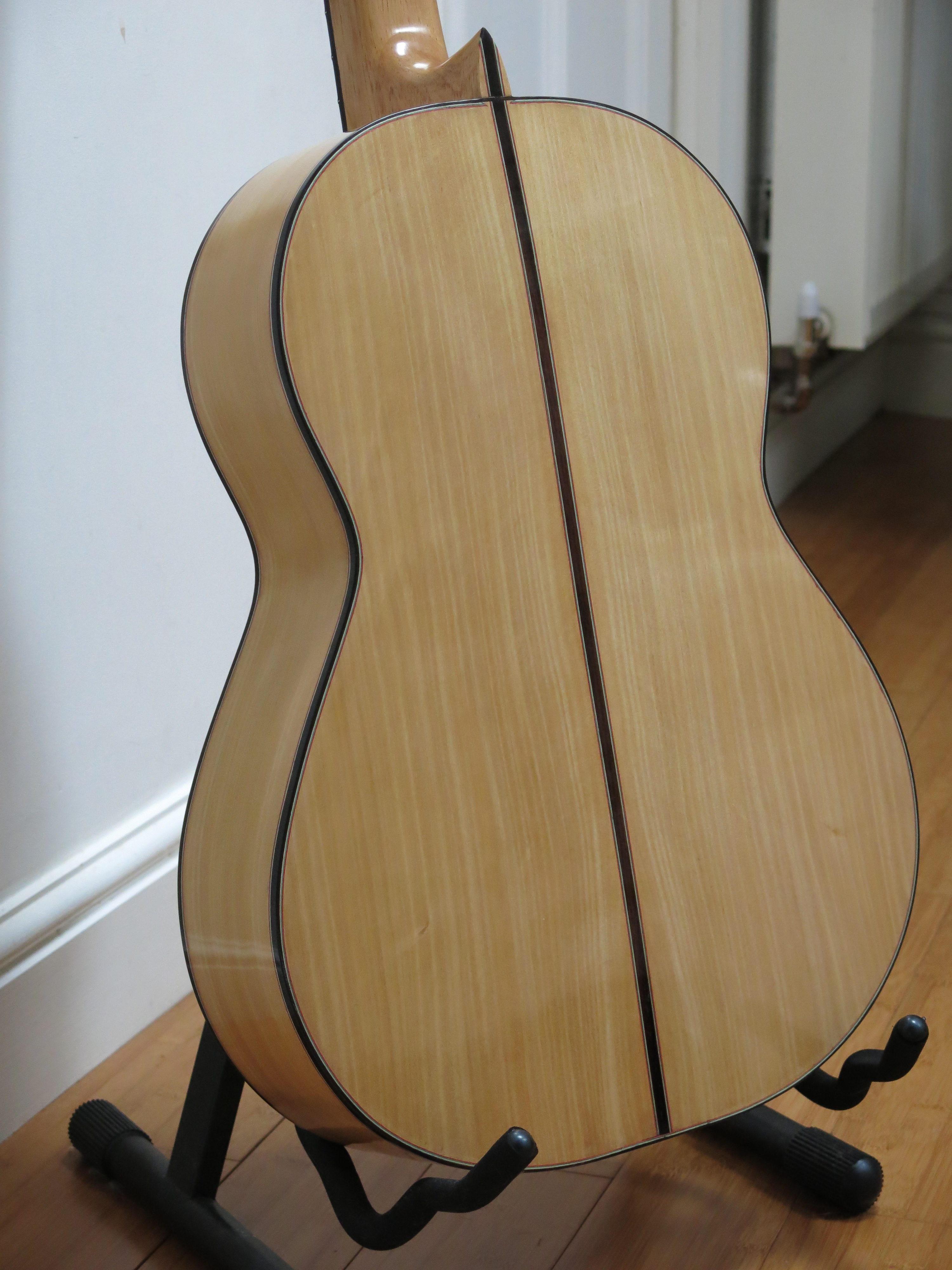
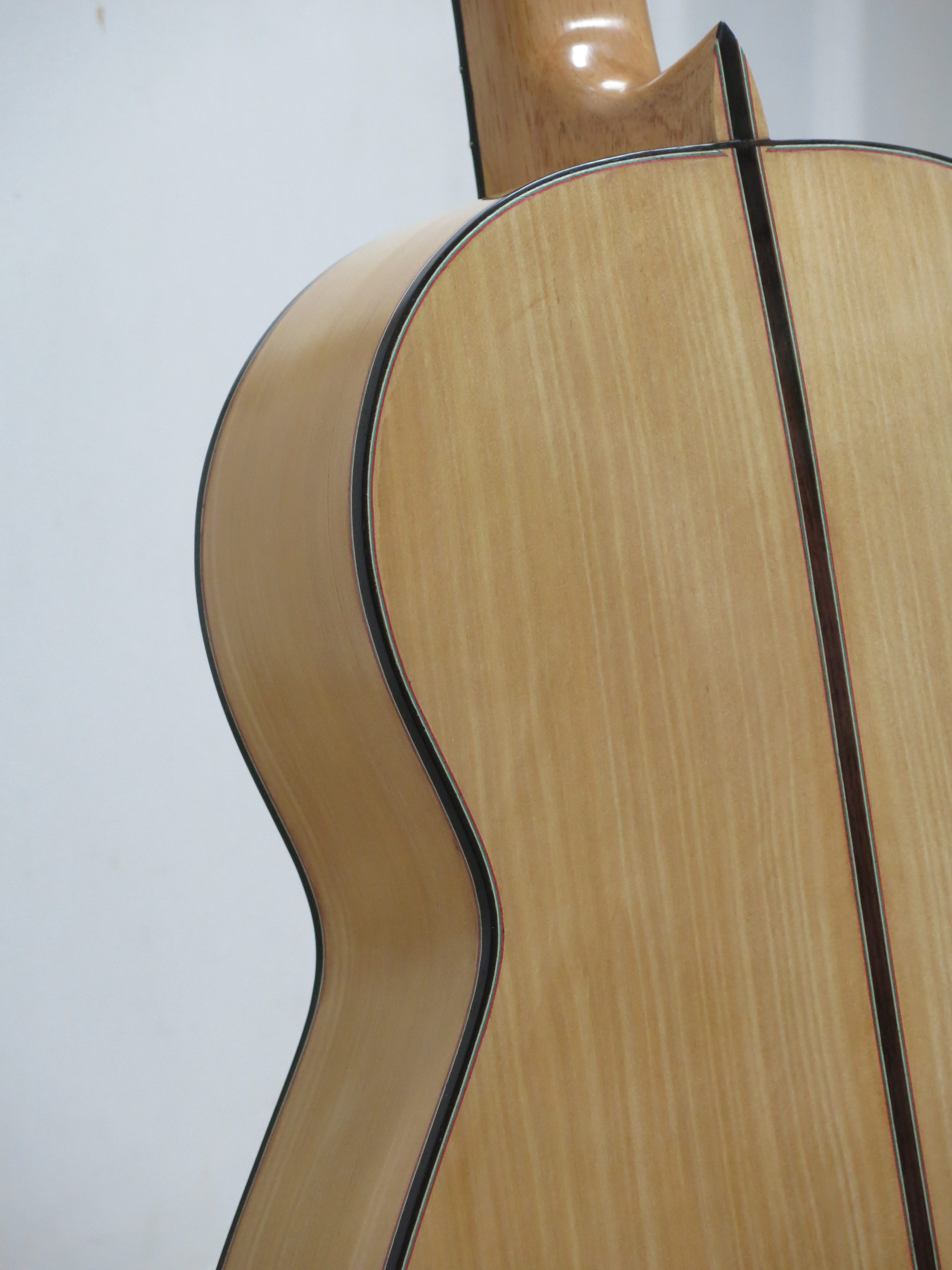
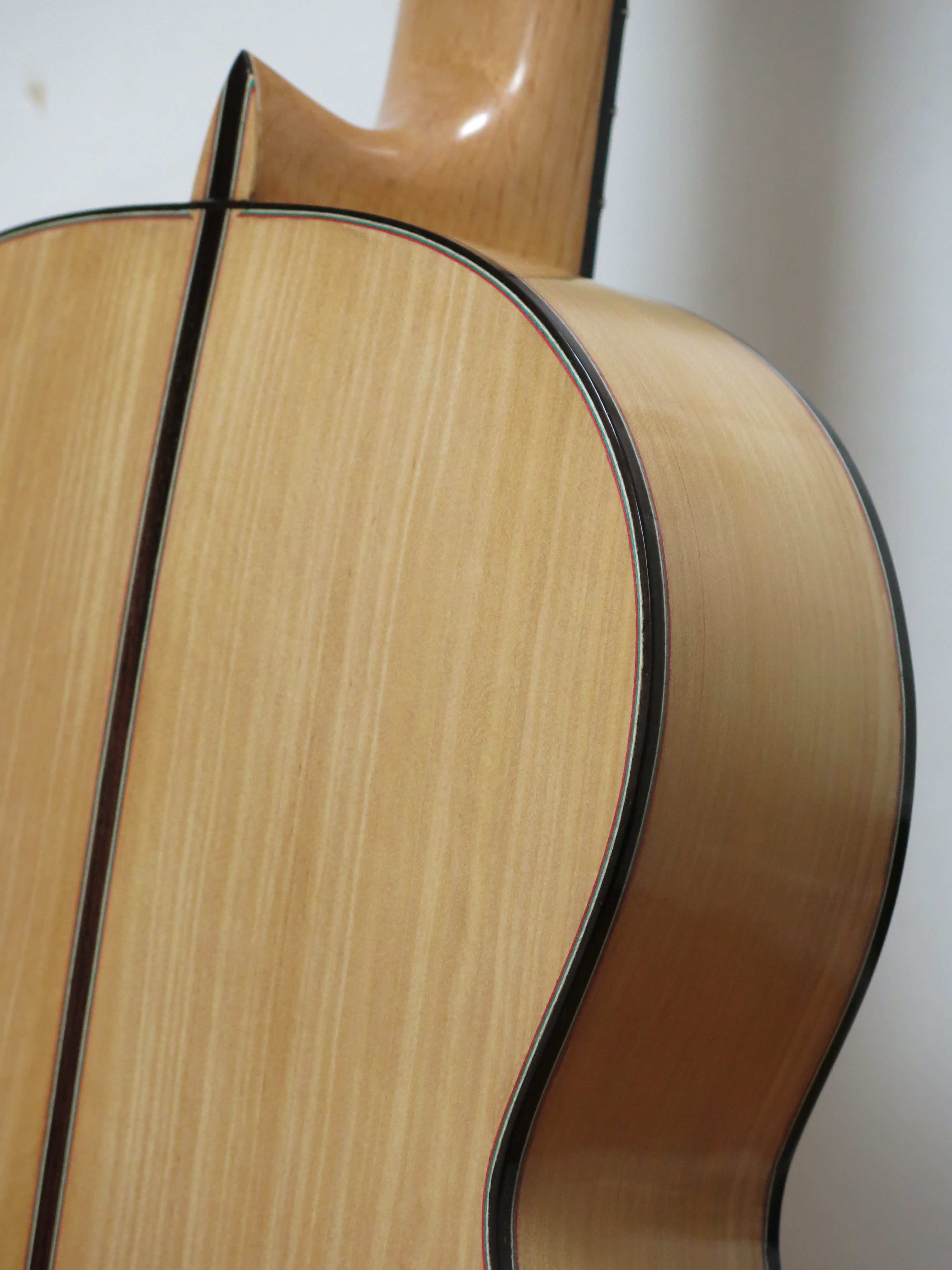
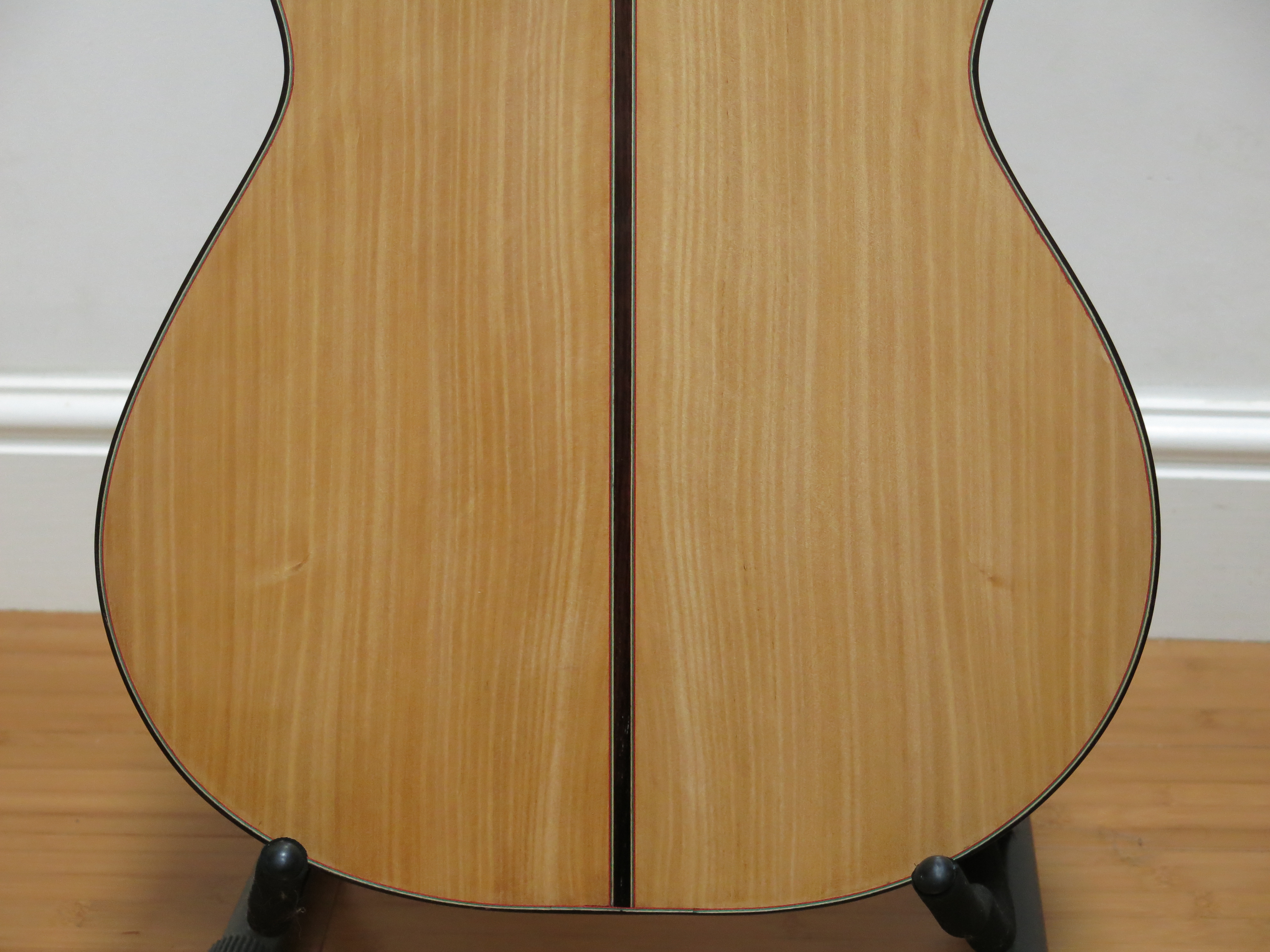
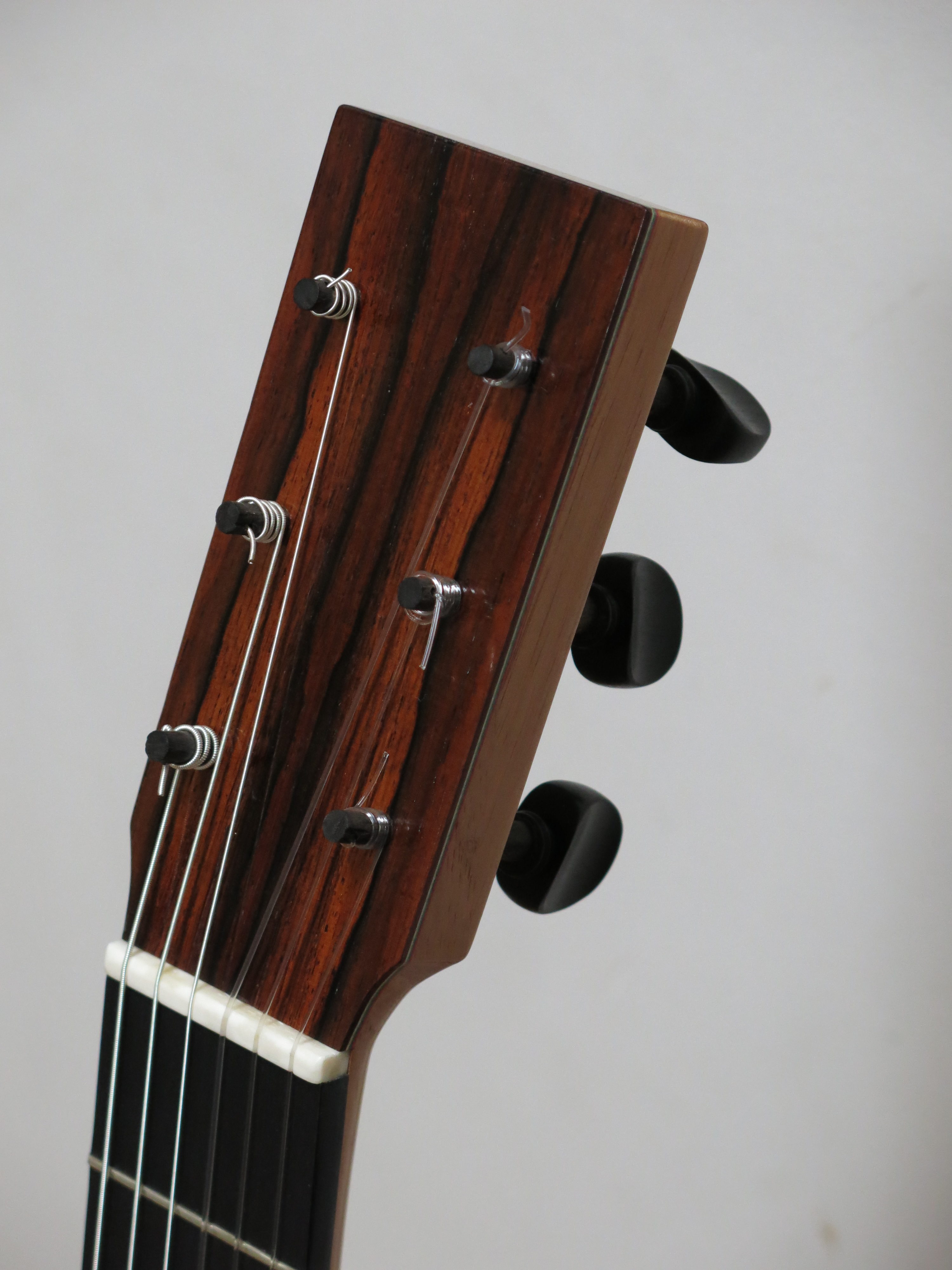
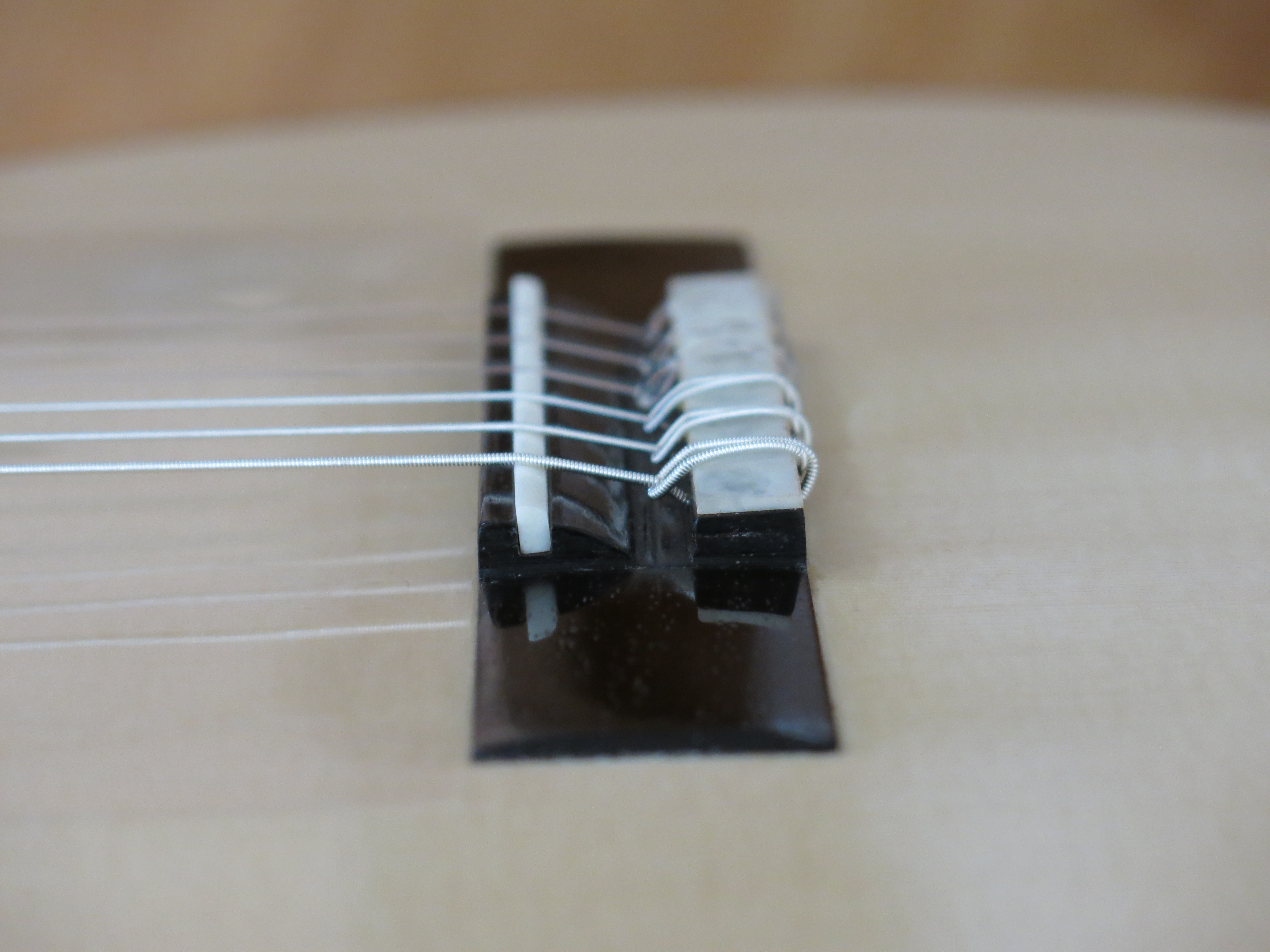
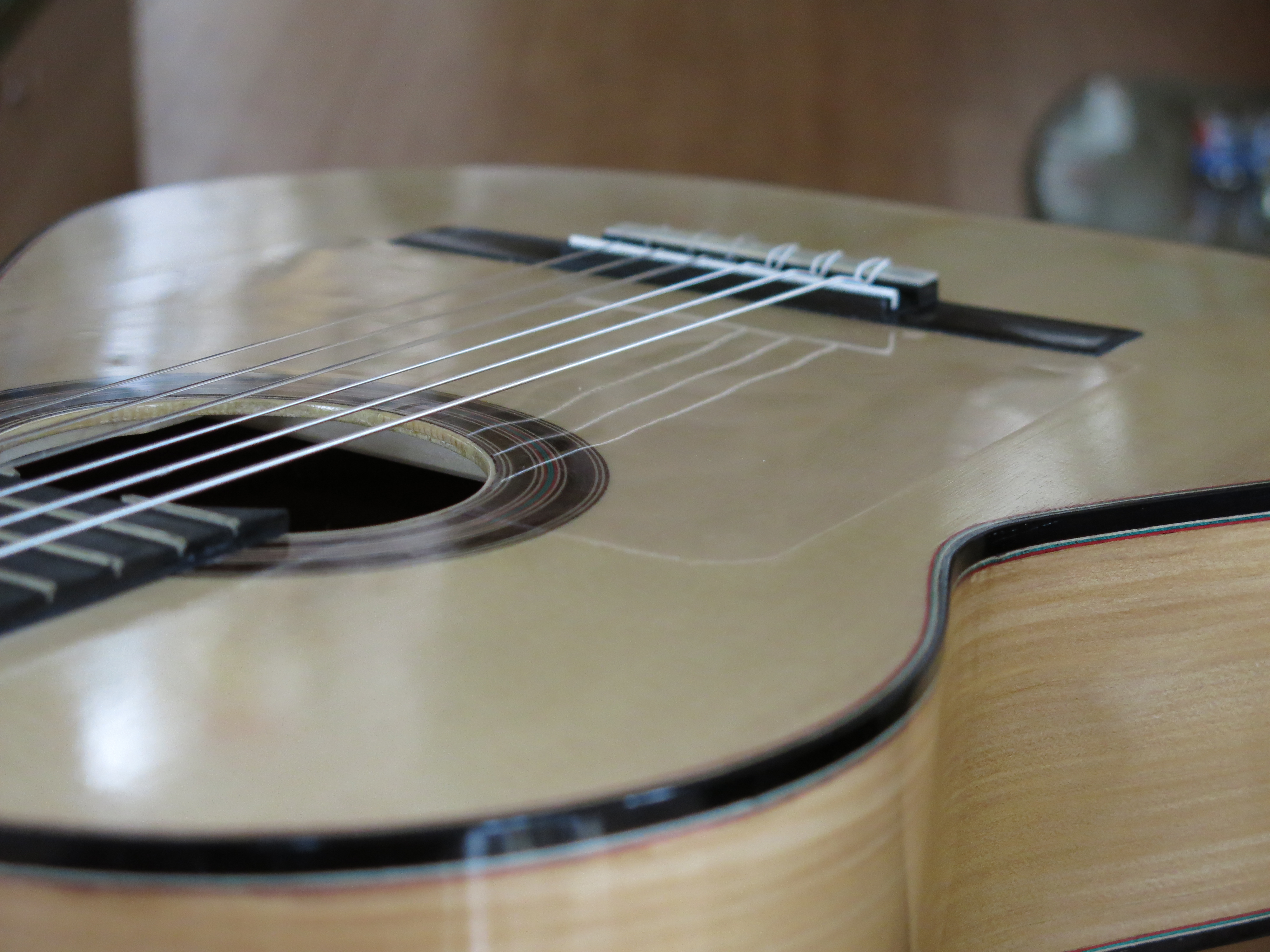
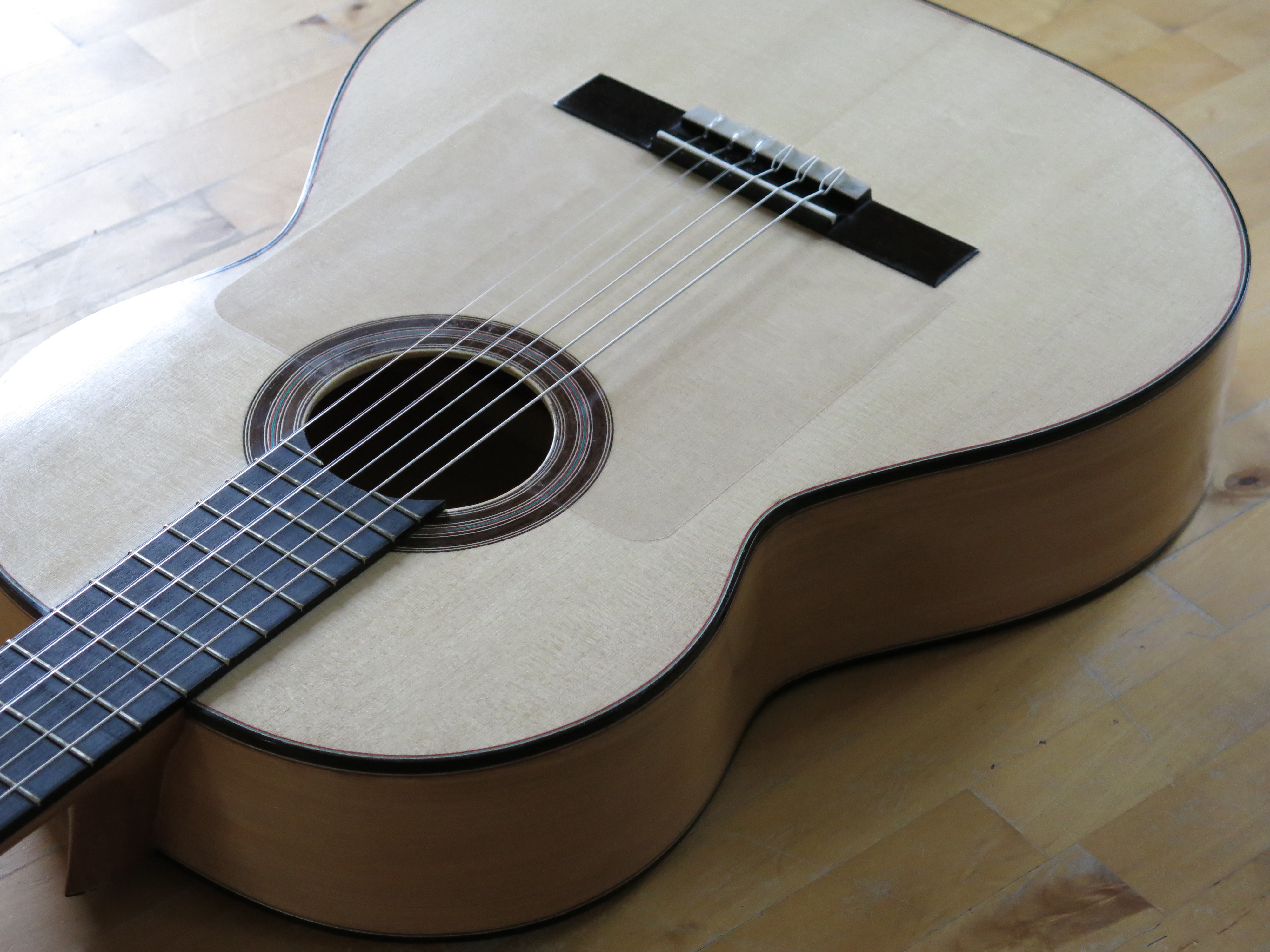
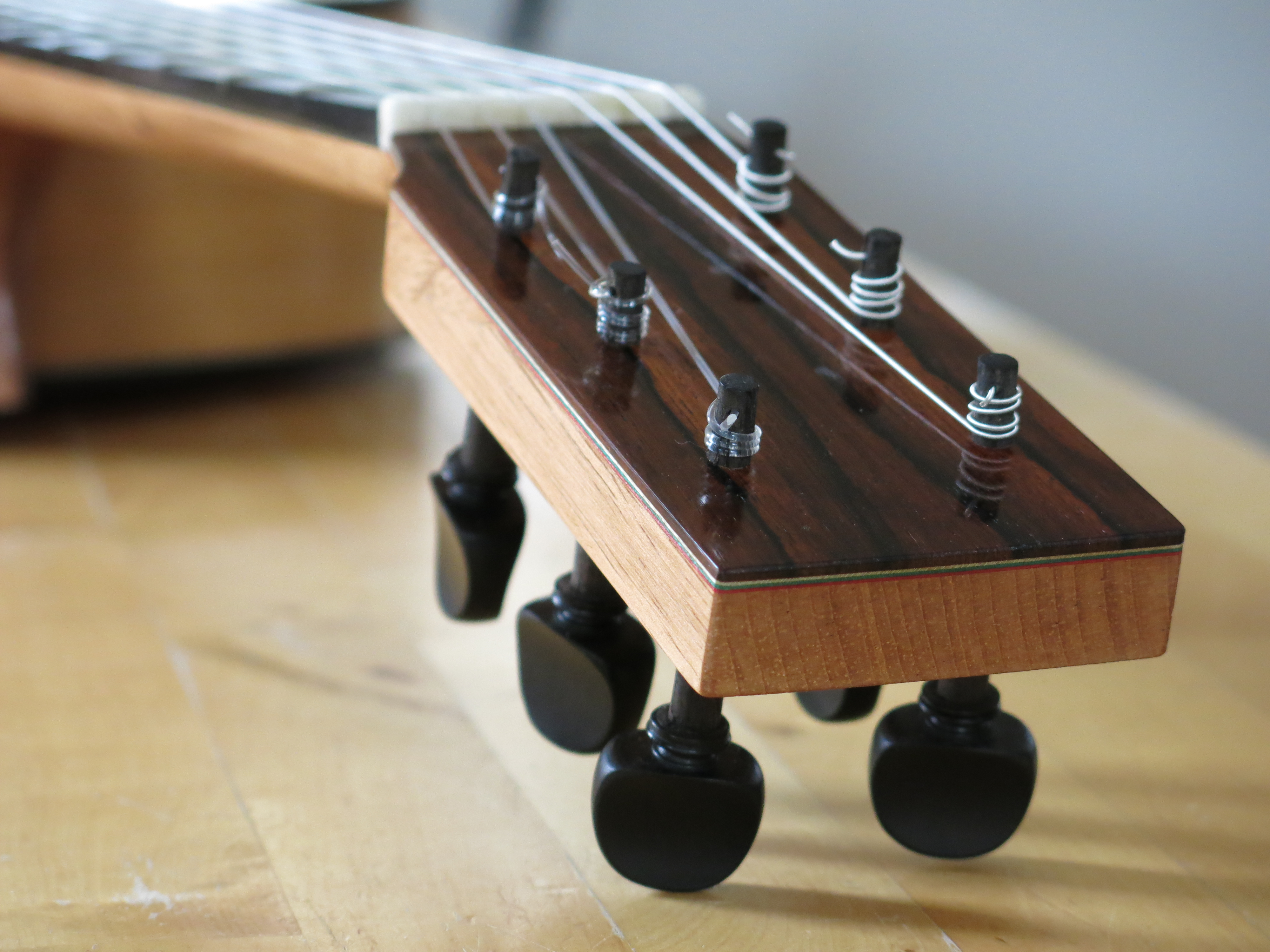
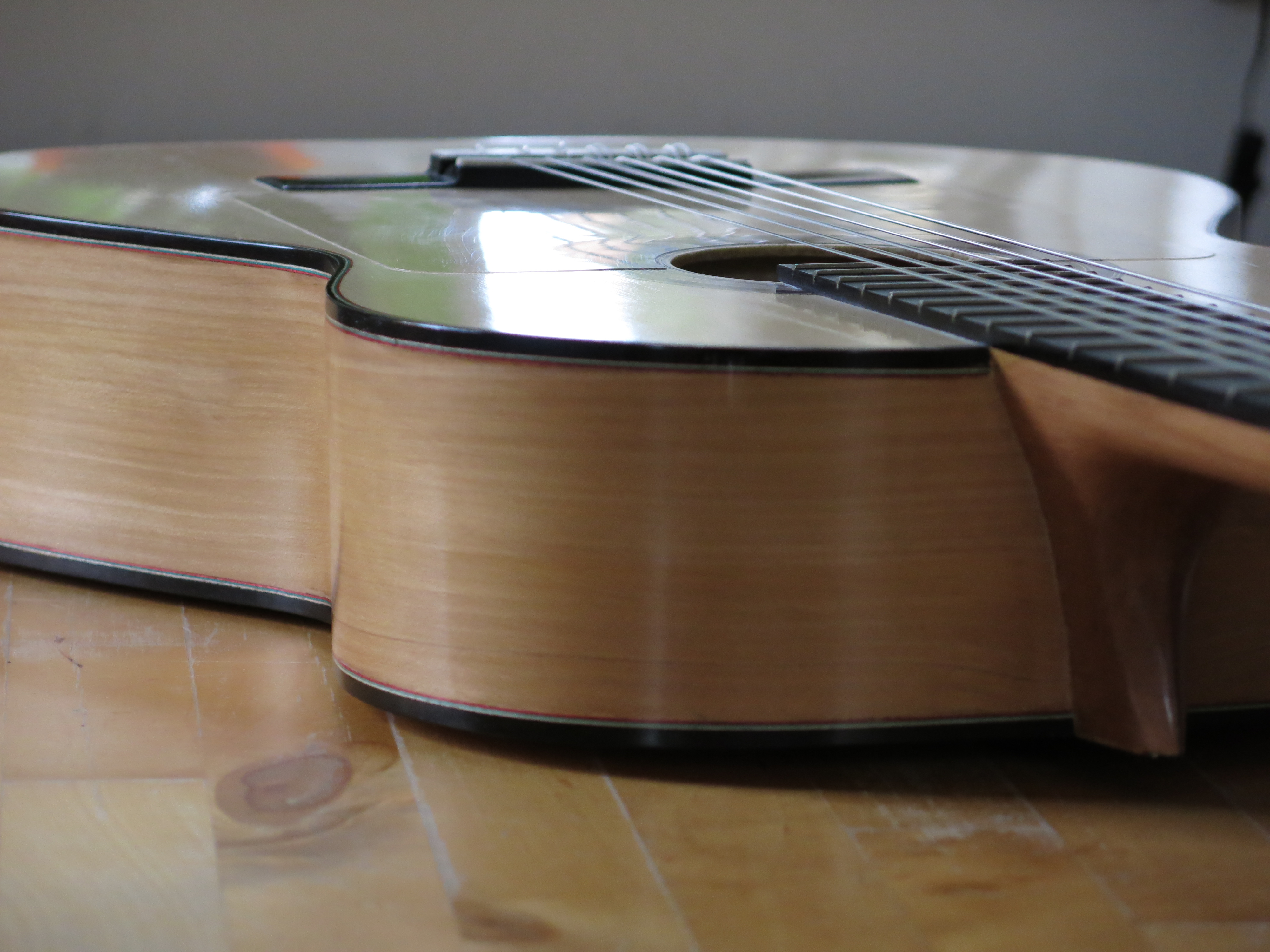
The back and sides are cypress, the top is engelmann spruce, the neck is Spanish cedar with a rocklite fingerboard, and the bridge is Madagascan rosewood. It differs slightly from #2 in that the back braces and end block are spruce, rather than Spanish cedar and the previous fingerboard was rosewood. I tried to advance my decorative skills a little more with #3 by making and inlaying a red/green/white purfling and back inlay that carries onto the heel. The rosette is a copy of a Barbero rosette. Overall, the workmanship is an improvement on the last guitar although not at the level I am satisfied with.
The sound of the instrument will change as it is played in, but first impressions are very satisfying. My hope is to make flamenco guitars that have similar characteristics to the sound of this wonderful Siguirilla, played by Paco del Gastor. Turn up your speakers and listen to the first minute (or more!)1
My guitar has a very punchy ‘cut’, decent bass and clear trebles, and just a little sustain – more sustain than the previous guitar. Notably, the instrument is very loud. I’ll try to get a recording of it after it’s had a few weeks of being played.
Weight
The overall weight of the instrument is 1189g compared to 1119g for #2. I deliberately chose a pale, lightweight piece of cedar (with graphite rod and beech peg bushings) for the neck (448kg/m3) and adjusted the thickness of the back, sides and top according to the % difference in density compared to #2, but it still ended up being 70g heavier. The rocklite fretboard (801kg/m3) is around the same density of some rosewoods. The back and sides (626kg/m3) are 1.8mm and 1.6mm respectively, and the top (424kg/m3) is 2.2mm around the lower bout gradually moving to 2.5mm in the upper bout and 3mm around the soundhole. The very low profile rosewood bridge (980kg/m3) weighed 16g with the bone on the tieblock attached. The bridge measures 6.1mm in front of the saddle with 1.7mm wings.
My obsession with the weight of the instrument is partly because of the success of the previous guitar in terms of how it sounds and the weight of that instrument was influenced by an observation in Gore & Gilet’s books on the characteristics of classic sounding flamenco guitars, which they observed were around 1100g. My obsession with weight is also because without the cumulative intuitive knowledge, based on the experience of making dozens of instruments, I’m relying heavily on the basic material properties of the wood that I can easily record and adjust. For my next guitar, I intend to measure the stiffness of the wood as well as the density.
Tap tone
The body resonance of the previous guitar is 92.189Hz (F#2 -6 cents) and a top resonance of 191.78 (G3 – 38 cents). The new guitar has a resonance of 90.17Hz (F#2 -44 cents) and the top is 191.78Hz (G3 -38 cents). Almost identical. The body resonance on #3 guitar is in the middle of two fretted notes (F and F#) which is the ideal place for it to be so as to avoid ‘wolf’ notes.
Action and saddle height
In addition to the weight, another technical consideration was to improve on the action for this guitar because I ended up re-fretting guitar #2 to eventually achieve what I wanted. First, I looked for what data I could find and compiled a spreadsheet of 55 flamenco guitars, recording the saddle height and action at the 12th fret. The data came from the Solera Flamenca website. Here’s a summary of the data:
- Mean action and saddle height: 2.66mm and 7.78mm
- Median action and saddle height: 2.6mm and 7.8mm
- Mode action and saddle height: 3mm and 7.6mm
I realise that the data on each guitar is not necessarily how it left the workshop, but reflects the set up by the seller. I’m also assuming the data is accurate because people are spending large sums of money to buy instruments online and unseen, so when they receive them, the set up needs to be as described. I believe the action on that website is recorded with the bass E string.
Data on the weight of those guitars is not often recorded but looking at the weight of 16 cypress guitars from famous makers, the numbers suggest that Gore and Gilet’s sample of six guitars of around 1100g were slightly lighter than average:
- Mean = 1200g
- Median = 1210g
- Mode = 1290g
The scale length across the 55 instruments is consistent:
- Mean = 655mm
- Median = 655mm
- Mode = 655mm
The nut width is pretty consistent, too:
- Mean = 52.9mm
- Median = 53mm
- Mode = 52mm
I was interested to see whether there was anything characteristic about the set up of older instruments.
- For the seven pre-WWII guitars, the average action is 2.5 and saddle height is 7.6mm.
- For 28 guitars up to 1969, the average action is 2.6 and saddle height is 7.8mm.
- For 13 guitars made after 1980, the average action is 2.8 and saddle height is 8.1mm.
Again, the action and saddle height may have been adjusted and it’s quite possible that the nut and saddle have been replaced on some of the older instruments, but there does seem to be a trend towards a slightly higher saddle and action.
In the journal, American Lutherie, Richard Brune discusses flamenco setup and writes:
“Originally, all Andalusian Torres models had a low action, about 1/8″ or considerably less between the 12th fret and the string. In the 20th century beginning around the 1930s and continuing after WWII, due to the influence of Segovia and other classical players who were playing larger halls, the standard ‘classical’ action began to increase, culminating in the impossibly high actions seen on Ramirez instruments from the 1960s to the present. However, action is always a matter of individual preference. Many modern flamenco players use a very high action, as did Ramon Montoya for precisely the same reasons, to avoid buzzing. More important is the consideration of neck angle and setup with negative, neutral, or positive relief (back bow, straight, or up bow) which greatly affect the ‘percussive’ quality of the traditional flamenco guitar. Corollary to this is the height of the strings above the soundboard at the bridge, which again was always very low for all Spanish instruments until the advent of nylon strings in the 1950s. This relates to torque on the top, which directly relates to how thin the top can be made, and how lightly it can be braced. Again, traditionally the Spanish guitars were all very lightly constructed, but since the 1930s, beginning with Hauser, classical guitars have gotten thicker and more substantial, with higher actions, taller bridges, and heavier bracing.”
Brune, R. (2000) American Lutherie #61.
So, with all of this in mind, I wanted to more accurately design the action and saddle height into the build of guitar #3, aiming for a saddle height of 7mm and action at the 12th fret of 2.5mm, which I know Rob would appreciate. Just as importantly, I wanted the string height at the 1st fret to be as low as possible, too, without the open strings buzzing. This involved setting a neck angle of 1.5mm into the solera, tapering the underside of the fingerboard slightly between the 12-19th frets to fit the angle, and gluing the slotted fingerboard onto the neck. I then made and temporarily fitted the finished bridge, nut and saddle and planed the top of the fingerboard until a straight edge was 3.5mm above the surface, which would result in action of 2.5mm above 1mm fretwire. I also had to take into account the 2mm dome of the soundboard (which collapses to under 1mm without string tension using my chosen bracing pattern) and anticipate the amount the strings would pull the soundboard upwards. This put me in the region of where I wanted to be so I had enough room to make adjustments to the saddle and nut when the instrument was finally strung up. The finished instrument has a saddle of 7mm and action of 2.5mm, as I had planned.
Golpeador
Although a seemingly trivial thing, the golpeador or tap plate is something that I’ve spent a long time trying to figure out a method for fitting. There are basically three methods: using self-adhesive plastic sheets from luthier suppliers; using blank plastic sheet (0.15mm) from craft suppliers, cutting it to size and shape and gluing with white PVA glue; or using epoxy rather than PVA. I’ve tried the PVA and epoxy methods before on mine and other people’s guitars and prefer the epoxy method that Aaron Green outlined. The PVA never dried thoroughly for me, whereas the West System epoxy bonds slow enough to get all the air bubbles out and position the plastic perfectly, and then dries hard to produce a nice glassy tap. I like this approach, also, because it feels like the fitting of the golpeador is part of the build process – something I make – rather than an accessory that I fit. Incidentally, gluing the golpeador didn’t change the overall air resonance of the guitar, whereas gluing on the bridge lowered it by about 70 cents.
The next guitar
My next guitar will be another flamenco blanca but this time using non-tropical and local wood. Flamenco guitars are traditionally made from cypress because, as Richard Brune argues, it is the only suitable tonewood native to Spain and was therefore cheaper to produce instruments from. In the mid-to-late 19th century, when the Spanish guitar design was established by Antonio de Torres, most players were Gypsy flamenco players who required cheap, loud, percussive guitars to play in the cafes. The flamenco guitar is therefore basically a folk instrument and I want to see what I can produce that is faithful to my own context. I also want to see what a Western red cedar top will sound like using the same Barbero design. The back and sides will be aromatic Cedar of Lebanon, which is light and strong and looks similar to cypress (the set I have is 503kg/m3 and comes from a tree cut in the UK). The neck will be lime from the UK (545kg/m3), the fretboard will be English bog oak (922kg/m3), and the bridge (630kg/m3), bindings and head veneer will be English walnut. The WRC top I have is 347kg/m3. I’ll report back in 6 months!

- That album is a fantastic live recording of a private performance at the flamenco club in the town of Morón de la Frontera, Spain on 23rd August 1988. The liner notes are worth the price of the CD, which music subscription services sadly lack. The lyrics of that Siguirilla are as follows:
I slept so deeply.
My dearest mother
Has been taken away.
I slept so deeply
That I heard nothing.
Now let us fall on bended knee
For the coming of the Lord.
So he may receive
My dearest mother,
Let us all kneel down
For the coming of the Lord.
I pray to the Moon
High up in the sky
To grant my father rest,
For I love him deeply.
Beautiful work on the guitar! I too am an amateur builder but studied with a builder for a month in Spain to sharpen my abilities. It is exceedingly difficult to learn in a vacuum without some expert guidance. My month in Spain completely changed the outcome of my projects!
I know what you mean, Jim. I don’t think I could have got very far without first being taught. Perhaps if I had extensive cabinetmaking experience beforehand I could have figured it out, but lacking that I really needed someone to show me. I’m building my fourth instrument now and it’s just starting to feel familiar to me. Like I’m leading the build process rather than being led by it. Only just! Who did you spend time with in Spain? Stephen Hill?
Excellent and very complete presentation(Ángel Del Río,Puerto Rico)