UPDATE 15/09/20: I originally wrote about six flamenco plans but have added two more GAL flamenco plans by Tom Blackshear to the comparison spreadsheet.
I have also removed the original comparison table from this blog post because it was too difficult to read. Please refer to the spreadsheet.
~~
How do you learn to make a ‘Spanish guitar’? There have been a number of books over the years and at the heart of them is an instrument plan.
A milestone in Spanish guitar making outside of Spain came in 1954, with the publication in Guitar Review of a scale drawing of Torres FE26 by Theodorus M. Hofmeester (1897-1955). For the first time, the design features of the Spanish guitar were plain to see and widely available to guitar enthusiasts to study and copy. Hofmeester was an Architect and President of the Classical Guitar Society in Chicago. Although the authenticity of FE26 has been called into question,1 nevertheless, the drawing provided a useful level of detail for subsequent makers to learn and build from. Although published in the USA, Guitar Review had readers and contributors in the UK and the Hofmeester drawing laid the groundwork for subsequent DIY texts on classical guitar making in Britain.
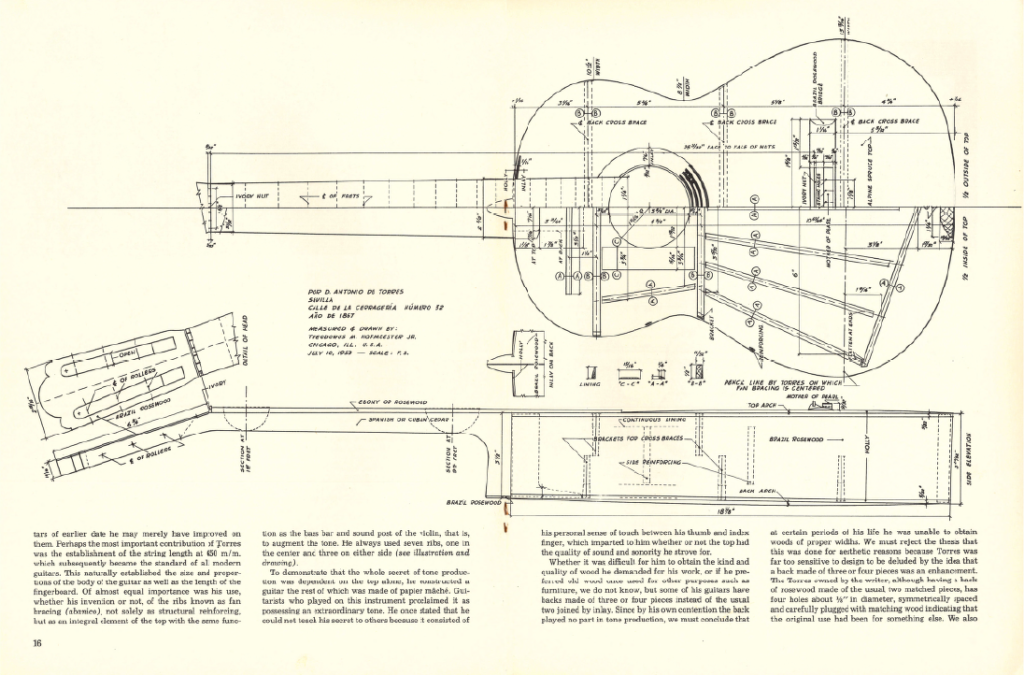
There is understandably a lot of emphasis on ‘learning by doing’ and ‘tacit knowledge’ in craft activities, with the use of books and scale drawings often overlooked. Guitar-makers don’t just do and their knowledge is not only intuitive. They observe, think, measure, study, plan and document their work.
In my survey of classical guitar makers in the UK, I asked ‘to what extent have you learned from the study of other instruments?’ Over 55% of respondents said they had learned ‘a lot’ or ‘a great deal’. Only around 5% said they had learned nothing at all from the study of other instruments.
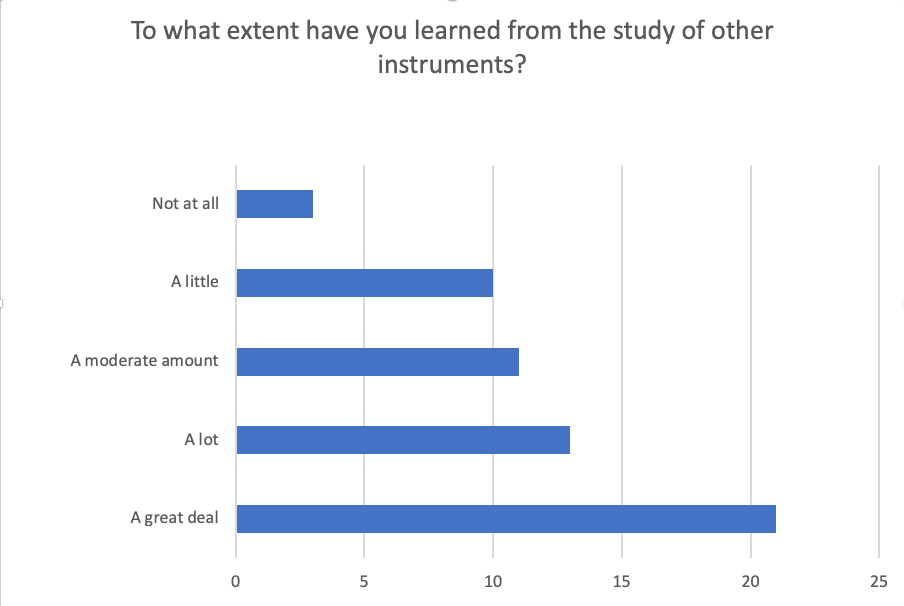
At some point, sooner or later, the student luthier will either study a ‘historic’ instrument (by which I mean, a guitar by an acclaimed, often deceased maker, whose instruments are prized by players and collectors) or, more often, study a drawing of a historic instrument.
Locating an instrument by an important maker is not always straightforward. They may be commercially available for tens of thousands of pounds or held in private collections. Occasionally they are held in museums, yet in the UK, there appear to be just two Spanish made guitars based on the Torres design in publicly accessible museums. Equally depressing, classical guitars made in the UK hardly feature in UK public collections either.
So, the alternative to an actual instrument is to study a scale drawing. There are a number of places to buy such plans and the detail and utility of them varies. Below, I evaluate six eight plans for flamenco guitars made by three influential Spanish makers, whose historic instruments sell for unadvertised prices today.
In evaluating the six eight flamenco plans, I will be guided by the article written by John Ray et al. (2017) ‘A review of basic procedures for an organological examination of plucked-string instruments’. The ‘basic procedure’ represents the most comprehensive published methodology available for examining and documenting guitars and other plucked string instruments. John Ray is a well-established Canadian guitar-maker and author who has lived and worked in Spain since 1989.
My objectives in evaluating the six eight plans are to compare them to the procedures described by Ray et al., discuss the strengths and weaknesses of each, and highlight what can be learned from the study of them collectively. I believe everything I have to say is applicable to plans of other types of guitar and possibly other instruments, too.
The six eight plans are as follows:
A: Santos Hernandez 1934, drawn by David Merrin
B: Domingo Esteso 1934, drawn by David Merrin
C: Santos Hernandez 1934, drawn by Richard Bruné
D: Marcelo Barbero 1951, drawn by Richard Bruné
E: Santos Hernandez 1933, drawn by Roy Courtnall
F: Marcelo Barbero 1950, drawn by Roy Courtnall
G: Manuel Reyes 2003, drawn by Tom Blackshear
H: Arcángel Fernández 1982, drawn by Tom Blackshear
Introduction to the drawings
On the face of it, the instruments are very similar, being Cypress bodied flamenco ‘blanca’ guitars made by Spanish luthiers between 1933 and 1951. In fact, there were personal connections between each maker: Santos Hernandez worked alongside Domingo Esteso in the Manuel Ramirez workshop, and Marcelo Barbero was hired by Santos Hernandez’s widow to complete the instruments he left unfinished after his death in 1943. Each maker is revered and any collector of classical or flamenco guitars would be pleased to own any of these instruments.
The plans by Roy Courtnall are CAD drawings made in the early 1990s with permission from dealer, Ray Ursell. The Santos Hernandez plan is also published in Courtnall’s book, Making Master Guitars, which features an introduction to the maker and his work. The Barbero plan is not included in the book and includes no accompanying biographical notes.
By comparison, the plans by David Merrin are reproductions of hand drawings of instruments from the Granary Guitar collection in 2011. The Granary Guitar Collection is well-known among players and luthiers in the UK because the owner has held open days to visit the collection.
The Richard Bruné plan of the Barbero guitar is hand-drawn and accompanied by extensive notes on the provenance of the instrument. It was featured in American Lutherie #55 and regarded by Bruné as “the defining flamenco guitar of the 20th century” because it was played by Sabicas on his album Flamenco Puro. Bruné’s plan of the Santo Hernandez instrument was published more recently in American Lutherie #73 and is a CAD drawing, again with accompanying notes on the plan and a related article in the same journal.
Basic Measurements for an Organological Examination
Ray et al. provide a list of measurements and features to document when examining an instrument, which I list below in order to indicate whether the six eight plans provide that information.
I am not able to reproduce the rest of Ray et al.’s article here, but can say that it contains various illustrations and images to demonstrate the procedure to capture this information as well as the tools required. It is a very thorough, practical guide on what to document and how.
I should also say that Courtnall, Merrin and Bruné did not necessarily set out to document the instruments for the same purpose as Ray et al. are proposing, and this evaluation is not intended as a criticism of their efforts, which I have benefited greatly from in my own workshop.
A: Santos Hernandez 1934, drawn by David Merrin
B: Domingo Esteso 1934, drawn by David Merrin
C: Santos Hernandez 1934, drawn by Richard Bruné
D: Marcelo Barbero 1951, drawn by Richard Bruné
E: Santos Hernandez 1933, drawn by Roy Courtnall
F: Marcelo Barbero 1950, drawn by Roy Courtnall
G: Manuel Reyes 2003, drawn by Tom Blackshear
H: Arcángel Fernández 1982, drawn by Tom Blackshear
Each plan is a 1:1 scale drawing so where measurements are not explicitly given, they can be more or less found by measuring the drawing itself. All measurements in the plans are in millimetres.
For a detailed comparison of all eight plans, please see the spreadsheet here.
Discussion
As you can see, each of the plans provides a lot of detail for the guitar-maker and, from experience, I know that a guitar can be made with the information given in any single plan.
The evaluation reveals something about each author’s motivation and approach. Merrin’s plans are the most comprehensive drawings for the guitar-maker; Brune’s plans are also comprehensive and show more scholarly concern for the provenance and condition of the guitar – something which Ray et al. are concerned with, too. Brune’s plans are perhaps best seen as studies of the instruments, as well as workshop references. Courtnall’s plans are primarily intended for the workshop and provide suggested thickness ranges for top and back rather than specific numbers, recognising that each piece of wood requires an assessment of its own attributes. The layout of Courtnall’s CAD plans are clear and easy to follow.
No single plan meets every expectation of Ray et al.’s procedure for examination but it would not take too much additional effort for future authors of instrument plans to adopt their procedure in full. Merrin and Courtnall’s plans do not provide specific dimensions for the top and back outlines and they assume the back is the same dimension as the top. Indeed, it should be and for a workshop drawing, we do not need the back outline dimensions. Bruné provides back dimensions for the Barbero (D), probably because of the guitar’s historic significance and also because it appears the different top and back dimensions was intentional. Similarly for the neck relief on the Barbero (D) guitar, which is in fact convex rather than concave, or ‘negative relief’ as Bruné refers to it.
In my own experience of building four flamenco guitars, using the Courtnall (F) and Bruné (D) Barbero plans, I thought it would be nice to have the weight and the main air resonance (Brune provides the air resonance but not the weight) These are both objective measurements that are easy to obtain and revealed to the maker with the finished guitar. They result from the maker’s overall creative effort, rather than any single detail on the plan and allow the luthier to compare tactile and aural attributes of the original guitar with their own. Merrin’s plans (which I bought very recently) include the weight and air resonance.
Beyond the six eight plans
While learning to build flamenco guitars, I have also been guided by the information provided by Trevor Gore, where he analysed the weight and resonance of six eight classic flamenco guitars. Where flamenco plans include the weight, we should be aware that older guitars are likely to have had wooden pegs rather than mechanical tuners, and if the pegs have been replaced by mechanical tuners, the published weight is around 100g heavier than it would originally have been. John Ray has a useful article on this.
In addition to the six eight plans for flamenco guitars, I have found Sheldon Urlik’s book to be informative because of the detailed measurements given on 82 “fine Spanish guitars” including 21 flamenco guitars. I have calculated the average measurements for the flamenco guitars in this spreadsheet for ease of reference and comparison. (On a separate worksheet there is also data taken from guitars for sale on the Solera Flamenca website). Looking across the average data for those 21 guitars, reveals the design attributes which make a flamenco guitar sound and feel like a flamenco guitar. They are very lightweight, the plates and ribs are thin, and the bridge is low. If you know anything about flamenco guitars, you knew this already, but the numbers really emphasise the importance of building within those parameters.
Having six eight plans to study is better than one, but not because the plans are significantly lacking. Having six eight plans helps you understand that the work of a single luthier will vary and that there is not just one way of making the same type of instrument. For example, it shows you that the brace does not have to be exactly that height, because on other guitars, it is a different height. Having six eight plans shows you that there is room to relax and work with the materials and not just with the plan.